Perfect Monit
All in real time
Allows the production monitoring through bar code; allows in every moment to dispose informations on the real progress state of the order and allows to make an effective analysis of production cost linked on every single resource. The made monitoring allows also a correct estimate of the production potential of each resource, either on usage of production programming module and on costs analysis.
Does
- The production progress control on each resource, detected in real time through reading of bar code on the various production areas.
- The auto-learning of the productive capacity of each resource, for every material category, in order to improve the times and production costs estimate.
- The automatic management of the breaking events.
- The monitoring for cut activity.
- The monitoring for machining phase (generic).
- The monitoring for tempering phase.
The monitoring results can be visualized from Perfect GePro work stations of the office. From here, it is possible in every moment to know which is the situation of work progress. This allows to make a decision on organization or to comunicate informations on order state to the customer without having to physically research the informations.
Last but not least allows to consider the work quantity on the system analysing the times registered by operators.
Monitoring for cut activities
The monitoring for cut activities allows to operators in production to comunicate to Perfect GePro the state of a project in progress on cutting machine that can be started / in pause / finished.
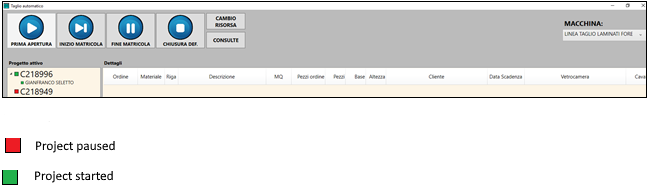
The module menu includes:
- First opening to open cut activity on selected machine.
- Activity start of the worker.
- Activity end of the worker.
- Definitively closing to close the cut activity.
Monitoring for generic activities
The monitoring uses the order print with the machining sequence after the cut, a print for each different “way” of the order (example: a print for each material). In addition to worker the order and the interested phase are inserted. At the closing of the phase it is possible to insert actually machined pieces, breakings and defective pieces.
As an alternative to the monitoring described above, it can be use Perfect Machine Interface or Perfect Code Client / Server monitoring